Imagine that every incident at your plant is captured in real-time, with critical data available instantly, eliminating any wait times. Where each production process is under control, and defects are spotted immediately, free from human error. Where you can swiftly investigate issues and track missing products, all without unnecessary bureaucracy!
Such consistent monitoring isn’t as easy as it sounds. In pilot tests of 3DiVi Omni Analytics at large-scale enterprises (with revenue exceeding $10 million and 400+ employees), we found that, even with surveillance systems in place, only 2.5% of work processes were actually analyzed, leaving the majority of video footage untouched.
Traditional methods like manual video reviews or working-day timing inspections fail to give a clear, objective picture. Employees aware of surveillance may adjust their behavior, disrupting normal processes and leading to increased defects when continuous monitoring is absent.
In this article, we'll look at four manufacturing problems that often go unnoticed but can lead to significant business losses. Video analytics can solve them all by detecting real-time deviations and enabling quick responses to production incidents.
Problem # 1: Your Machines Sit Idle for Nearly 60% of the Workday
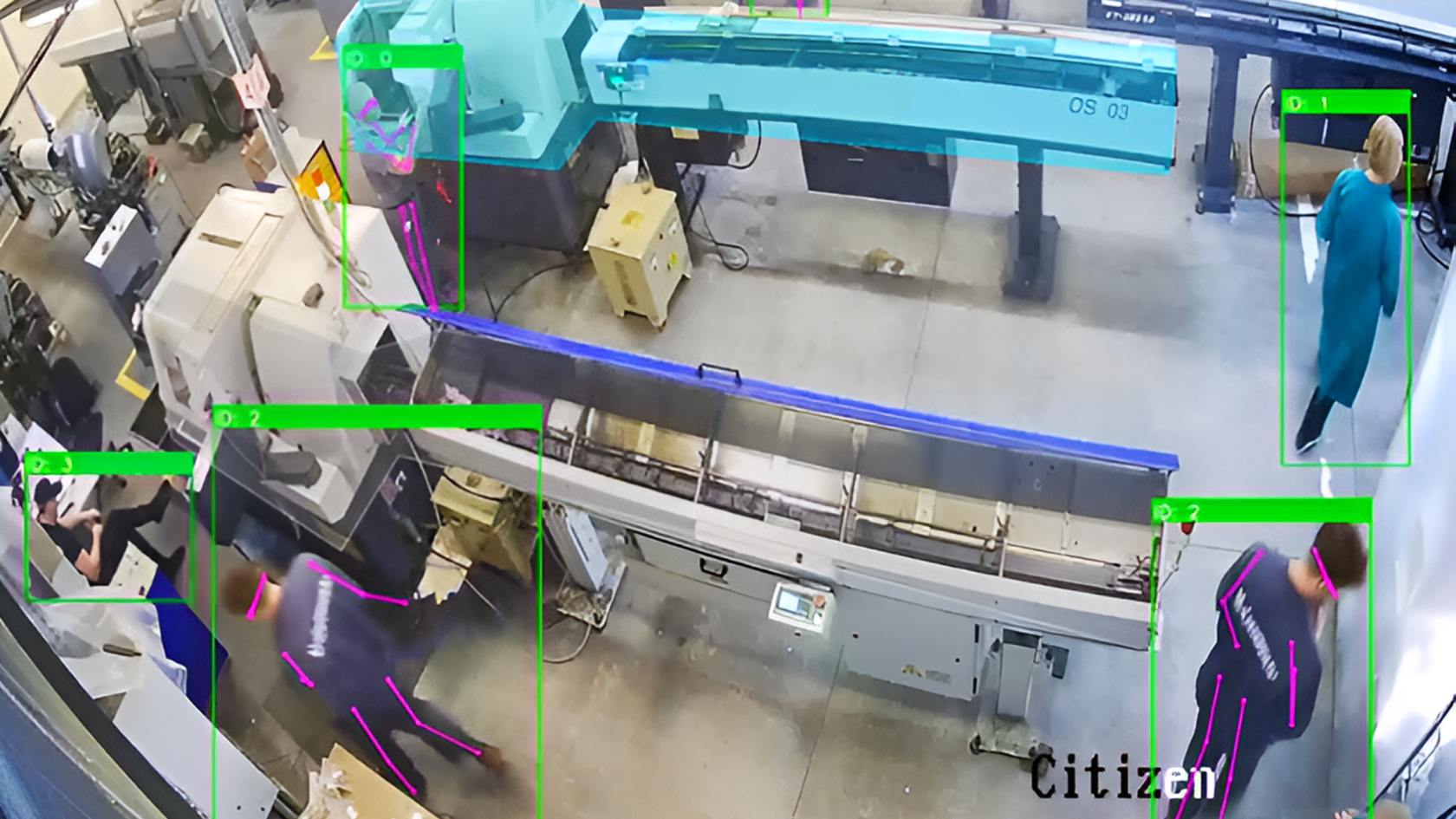
Many businesses don’t realize how much time their equipment is sitting idle. According to our clients, dispatch systems often reveal that equipment is unused for about 60% of working hours. Here’s the breakdown:
- Technological downtime: 37% (e.g., cleaning machinery, or inspecting parts)
- Unjustified downtime: 15%
- Setup-related downtime: 8%
In a recent pilot test at a factory, just 2 hours of machine operation revealed 25 instances of technological downtime, 8 unjustified downtimes, and several setup-related issues. Tracking and analyzing all this manually across 100 machines running 24/7 would be impossible.
This is where video analytics can make a difference. By monitoring factors like the operator's hand position, these systems help identify which events need attention and which don’t.
For instance, a long technological downtime could be justified if the operator’s hands stayed within the machine's work zone.
For instance, a long technological downtime could be justified if the operator’s hands stayed within the machine's work zone.
Problem # 2: Failed Technological Processes = Costly Defects
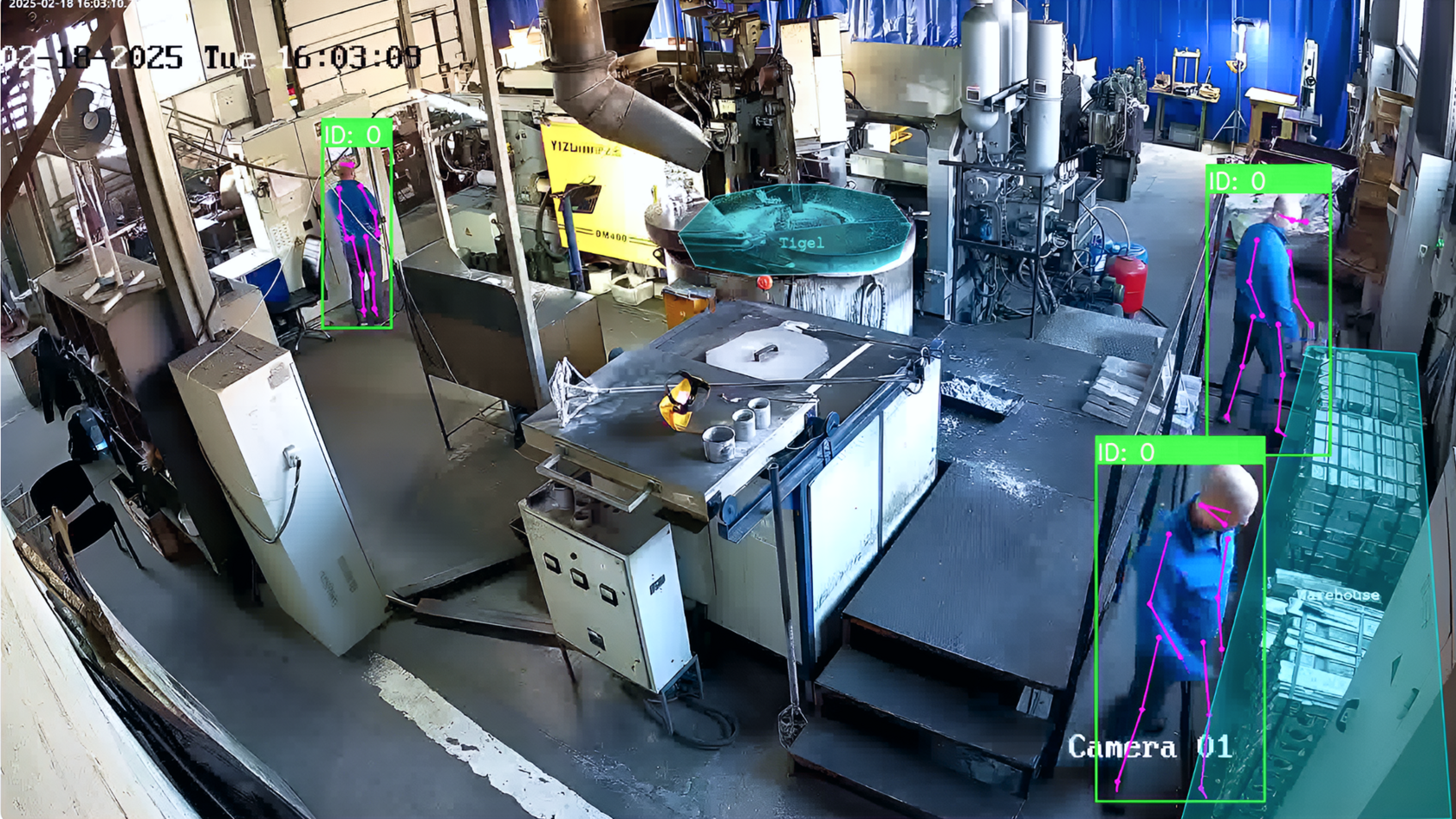
Video analytics can detect abnormal processes early, helping to prevent costly defects. Take foundry production as an example: mistakes at any stage can lead to defects and major financial losses.
By monitoring key stages of casting, video analytics can minimize defects, and adjust production operations. Here's how:
Raw Material Preparation
The system tracks when workers interact with storage zones for metal ingots and chemical additives, ensuring that each step is followed correctly.
For instance, before loading ingots into the crucible, it’s critical to preheat them. This helps prevent excessive cooling of the alloy in the crucible, which could halt the casting process until the crucible reheats. Preheating also helps vaporize any water present, which could otherwise explode during casting, creating bubbles in the alloy.
Video analytics also oversees the precise order in which chemical reagents are added. Metal casting is performed at 650°C, while chemicals are added at 730°C. The process begins with adding the ingots, followed by adjusting the temperature in the heating zone and waiting for it to reach 730°C.
Once the temperature reaches the desired level, the first chemical additive—a flux—is added to the crucible, and the slag is removed. The second additive, a degasser, is introduced next, allowing all gases to escape. Once the alloy cools to 650°C, the casting can begin.
Once the temperature reaches the desired level, the first chemical additive—a flux—is added to the crucible, and the slag is removed. The second additive, a degasser, is introduced next, allowing all gases to escape. Once the alloy cools to 650°C, the casting can begin.
Any errors in the sequence of adding reagents, temperature control mistakes, or missed steps can lead to defects. Video analytics monitors these processes, ensuring adherence to security protocol and preventing costly errors.
Monitoring of Castings
After each casting cycle, workers are required to inspect the castings for any signs of damage, such as scratches or marks on the product. Early identification of such defects is critical. If any are found, pressing must be halted to prevent further damage to both the alloy and the mold. Failure to do so could lead to expensive repairs or mold replacement down the line.
Product Detection in Specific Zones
3DiVi Omni Analytics includes a few-shot learning tool that quickly adapts video analytics for the detection of specific objects. For example, in foundry production, the system was trained to detect billets in the preheating zone near the furnace, as well as monitor the metal flow for injection.
Problem # 3: 5 Employees on Shift, but Only 4 Actually Get Things Done
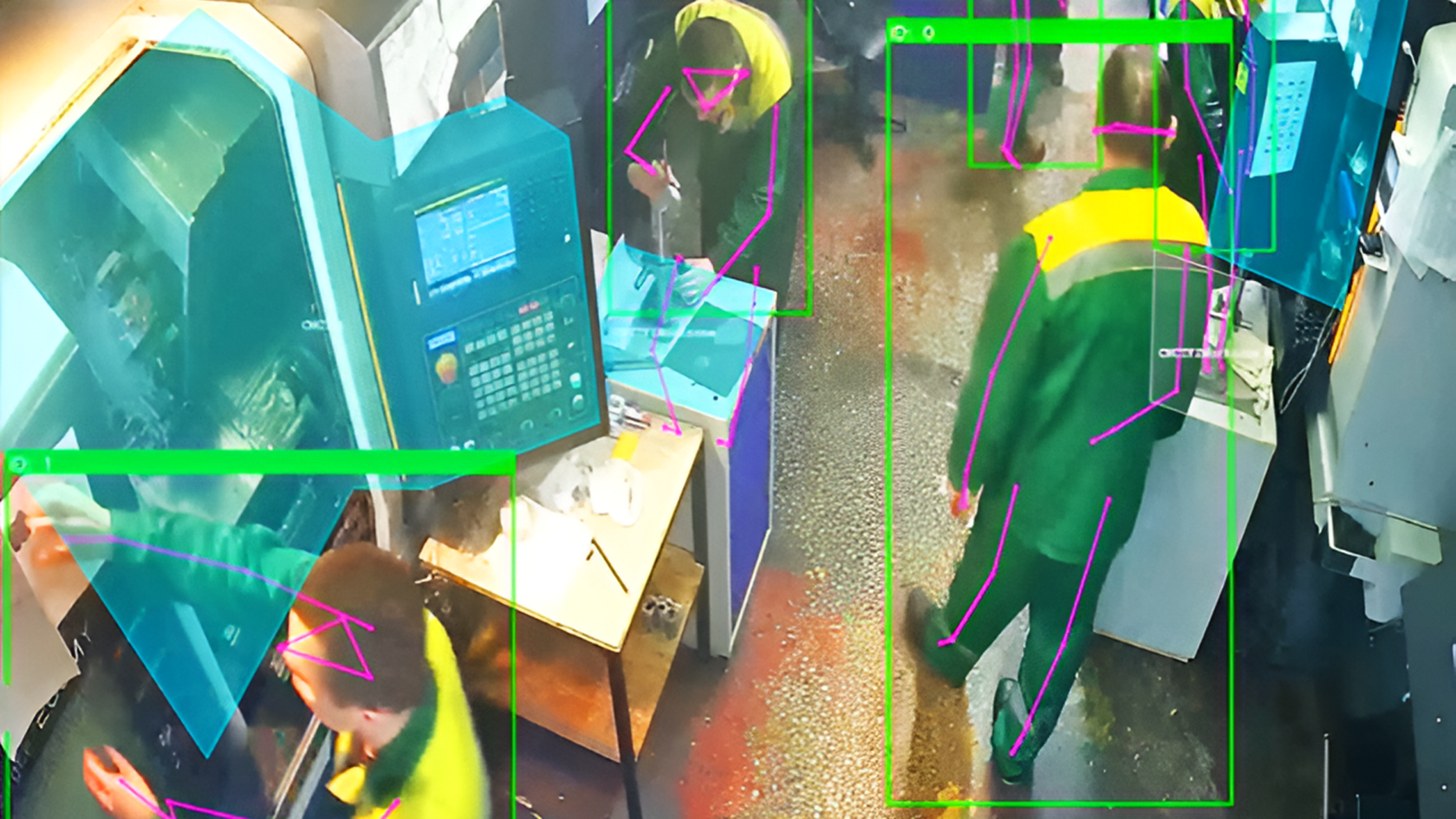
Video analytics helps improve workplace safety by identifying excessive crowding in production areas, which could potentially violate safety protocols. It also tracks prolonged, unjustified employee absences during shifts.
Problem # 4: Missing Tools? Now the Whole Team’s on the Hunt
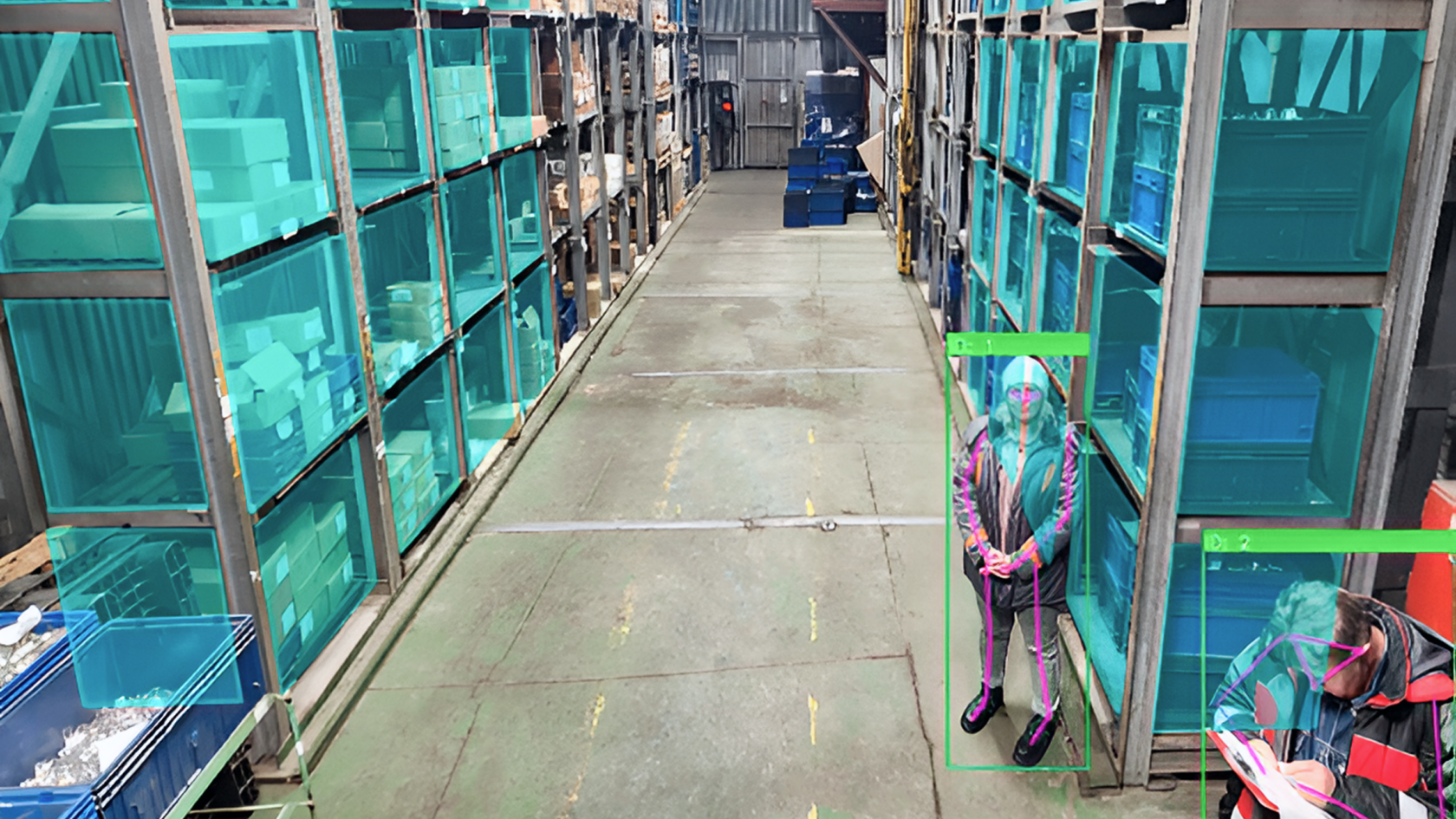
Video analytics tracks who accessed specific storage bins and materials, making investigations into missing tools much simpler. No more sifting through endless video archives or conducting manual searches.
With just a body detection system, commonly used in modern facilities, video analytics can capture the presence of a person near a storage bin or shelf, but it doesn't confirm whether they are interacting with it. By using skeletal tracking, we can precisely determine if the employee is engaging with that specific area.
Warehouse managers, dispatchers, and foremen often lack access to surveillance systems, as this typically falls under security’s responsibility. With video analytics, we can provide them with the necessary tools to oversee operations without compromising security protocols.
Final Thoughts
Video analytics does more than just strengthen safety and reduce equipment downtime—it uncovers hidden inefficiencies in the production process, helping to prevent costly defects. For large-scale enterprises, these solutions are invaluable, automating data analysis and driving greater operational efficiency.
Curious about how video analytics could improve your business? Reach out to us to discuss your project in detail and find the best solution for your needs.